Practical Knowledge of Corrugated Box Die-Cutting
- JF-PACK
- 2024年11月25日
- 讀畢需時 6 分鐘
已更新:2024年11月26日

The die-cutting technology of corrugated paperboard is widely used all over the world, mainly including two processes: flat die-cutting and rotary die-cutting. Among them, die-cutting includes three methods: flat-to-flat, rotary-to-flat and rotary-to-rotary die-cutting.
Flat-to-flat die-cutting
Flat die cutting uses a flat die and a flat die cutter. The blade cuts through the entire corrugated cardboard at the same time during die cutting. It has the highest die cutting accuracy and is widely used. It can be used for materials such as self-adhesive paper, cardboard, and corrugated cardboard. Flat die cutting machines are divided into vertical semi-automatic die cutting machines and horizontal automatic die cutting machines. Vertical die cutting equipment has a simple structure, convenient maintenance, easy operation and replacement of die cutting and creasing plates, but the process is labor-intensive and has low production efficiency. The number of working times per minute is mostly 20 to 30 times, and it is often used for small batch production and processing.The overall structure of the horizontal flatbed die press is similar to that of a sheet-fed offset printing machine. The whole machine consists of an automatic cardboard input system, a die pressing part, a cardboard output part, electrical control, mechanical transmission and other parts. Some are also equipped with an automatic waste removal device. The machine is safe and reliable in operation, with a high degree of automation and production efficiency.

Rotary-to-flat die-cutting
A cylindrical pressure roller is used instead of a pressure plate. Generally, the pressure roller is on the top and the die-cutting plate is on the bottom. The die-cutting is processed in a "line contact" manner, so that the pressure on the machine during die-cutting is small and evenly distributed, so the load of the machine is relatively stable, and a larger die-cutting can be performed. This method is suitable for die-cutting of products with different materials and thicknesses. However, most rotary die cutting machines have a stop-turn or one or two turns as one working cycle, so the efficiency is low and it is rarely used at present.

Rotary-to-rotary die-cutting
The rotary die-cutting machine has a continuous rotating die-cutting drum, so its production efficiency is the highest among all types of die-cutting machines. The die-cutting precision of the product is high and can be controlled within ±1 mm. At the same time, it has the advantages of simple operation, safety and reliability, and long service life. As for the die-cutting equipment for post-printing processing of corrugated paperboard, rotary die-cutting has become the mainstream. The die-pressed plate is made of curved wood board and roller knife, which requires high strength of die-cutting knife. The production difficulty and cost of die-cutting knife are high, so it is suitable for large-scale production and processing. There are two types of round-to-round die-cutting methods: hard cutting and soft cutting. The main difference is that the material of the pressure roller is hard steel roller and soft plastic roller. Hard cutting means that the die cutter is in hard contact with the surface of the pressure roller during die cutting, so the die cutter is more likely to wear and curl. The soft cutting method is to cover a layer of engineering plastic on the surface of the pressure cutting roller. During die cutting, the cutter can have a certain amount of cutting in, which can not only protect the cutter but also ensure complete cutting. However, the plastic layer needs to be replaced regularly, otherwise the die cutting size will be inaccurate due to inconsistent line speed.
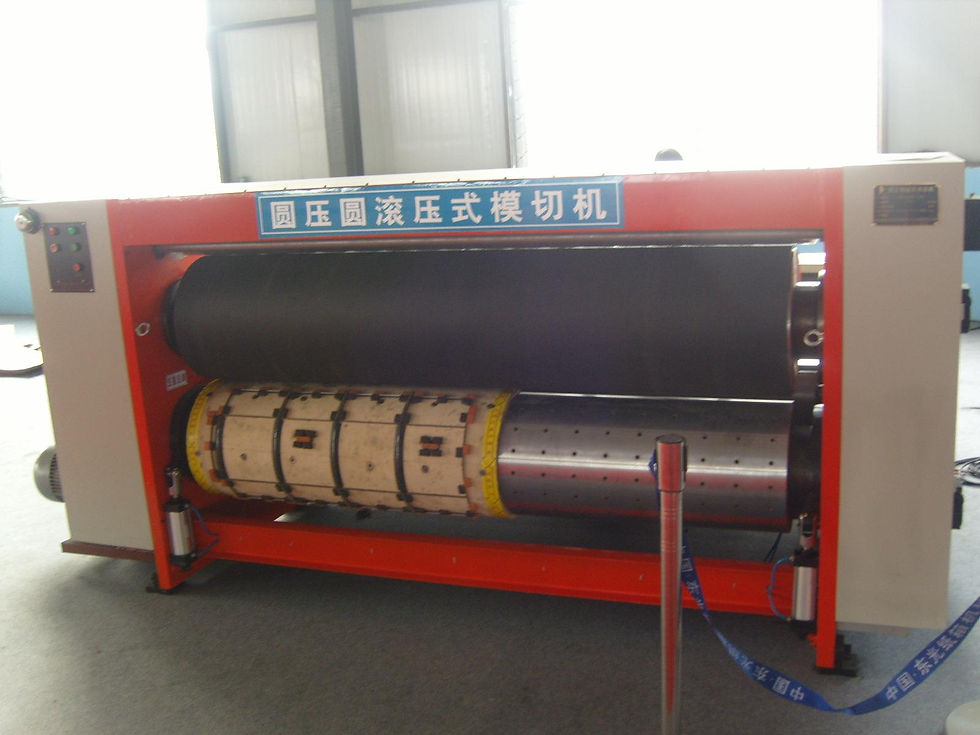
Common Die Cutting Marking Problems and Strategies
The position of the die-cutting indentation line does not match the position of the printed product
The production process of the die-cutting blade itself has errors. Manual plate making cannot achieve the ideal die-cutting indentation accuracy due to the limitations of the technical staff level and operating equipment. For some products that require high die-cutting accuracy, laser plate making can be used instead.
The gripping rules of cardboard vary. If the gripping specification error of the cardboard is large, it may be that the rear positioning (also known as secondary positioning) of the die-cutting machine is too small. This can be solved by adjusting the rear positioning and increasing the rear positioning toggle distance.
The die-cutting indentation is not aligned with the printed grid. The solution is to recalibrate the die-cutting plate according to product requirements and align the printed grid with the die-cutting indentation. In addition, you can also adjust the paper conveying side positioning rule or the front positioning rule to align the die-cutting indentation line with the printed grid.
In addition, the different working environments of die-cutting, creasing and printing will cause deformation or stretching of cardboard fibers, and inaccurate die-cutting and creasing grids. The solution is to try to ensure that die-cutting, creasing and printing are carried out in the same working environment or to ensure the same working environment (i.e., the same temperature, humidity, etc).
Insufficient die cutting precision
The main drive chain is worn and elongated, which will directly affect the positioning accuracy before die cutting. At this time, the only option is to replace the chain.
The intermittent mechanism is worn, causing the teeth row to shake during the stopping or starting process, thus affecting the die-cutting accuracy. In this case, it generally only affects the positioning accuracy. At this time, the intermittent mechanism should be repaired.
The positioning distance between the front and rear positioning swing frames is too small. Because the length of the chain itself has a certain error, if the positioning distance is too small, the chain error cannot be eliminated during the front and rear positioning, thus affecting the die-cutting accuracy. At this time, the adjustment screw of the front positioning swing frame or the cam position of the rear positioning swing frame should be adjusted so that the front and rear positioning frames can move the tooth row 2 to 3 mm.
The upper or lower die-cutting plate is not positioned accurately. Long-term use of the machine will cause the positioning blocks on the die-cutting plate frame or die-cutting bottom plate to wear, resulting in excessive clearance and reduced die-cutting accuracy. At this time, the positioning blocks should be replaced.
The wear of the side positioning plate is an important factor causing inaccurate side positioning. Since the amount of positioning movement is not enough to compensate for the wear, the side positioning accuracy will deteriorate. At this time, the side positioning plate should be replaced.
The gripper pressure is too small or uneven. If the elasticity of the movable teeth of the gripper decreases due to long-term use, the paper will slip or fall off during the transfer process, which will directly affect the die-cutting accuracy; uneven pressure between the grippers may cause the paper to skew during the die-cutting process. In this case, the movable teeth should be replaced. In addition, the fixed teeth should also be consistent in horizontal height, otherwise there may be a collision of the paper when gripping the paper or the paper may wrinkle after gripping the paper, affecting the die-cutting accuracy.
During the operation, the cardboard deforms or stretches, causing inaccurate "registration", thus affecting the die-cutting accuracy. The appropriate paper should be selected to reduce the impact of the material's own defects on the die-cutting accuracy.
The operator makes an error in operation and the precision is insufficient, or the die-cutting plate itself is not accurate enough and the die-cutting precision does not meet the requirements. At this time, the operator should be professionally trained, the production management requirements should be improved, or the die-cutting plate should be remade.
Explosion of lines (color) at the indentation
Crumbling refers to the cracking of paper at the indentation when the product is die-cut or folded. This is a common problem in die-cutting, especially in dry weather. It should be analyzed according to the specific situation:
The paper is brittle and has low water content, especially the paper that has been polished at high temperature, which is easy to crack during die-cutting. In this case, moisten the paper before die-cutting. You can use a water machine to pass water on the back of the paper to increase its water content and make it slightly flexible before putting it on the die-cutting machine. If the paper cracks during box pasting after die-cutting, you can wipe water on the fold to alleviate the cracking condition.
If there is a large area of dark blue or black on the printed surface, it is easy to cause color or line bursting after die-cutting. When printing, add no or little ink additives to the dark ink to enhance the adhesion of the ink on the paper and reduce the phenomenon of color or line bursting.
When the thickness of paper (board) is too large, it is easy to produce cracking lines. At this time, the height of the die-cutting steel wire should be selected reasonably.
The steel plate is prone to bursting when paper is placed under it, so the paper should be made thinner.
When the pressure of the die-cutting machine is too high, the wire is prone to bursting. At this time, the pressure should be reduced so that the waste edges are just separated.
The indentation die or bottom touch paper is too thick, the indentation is narrow, and the line is easy to break. The indentation die of appropriate thickness should be selected, and the indentation width should be moderate.
The paper dust dropped from the cut accumulates in the slot and is prone to explosion. The operator should promptly remove the paper dust and foreign matter.
Comments